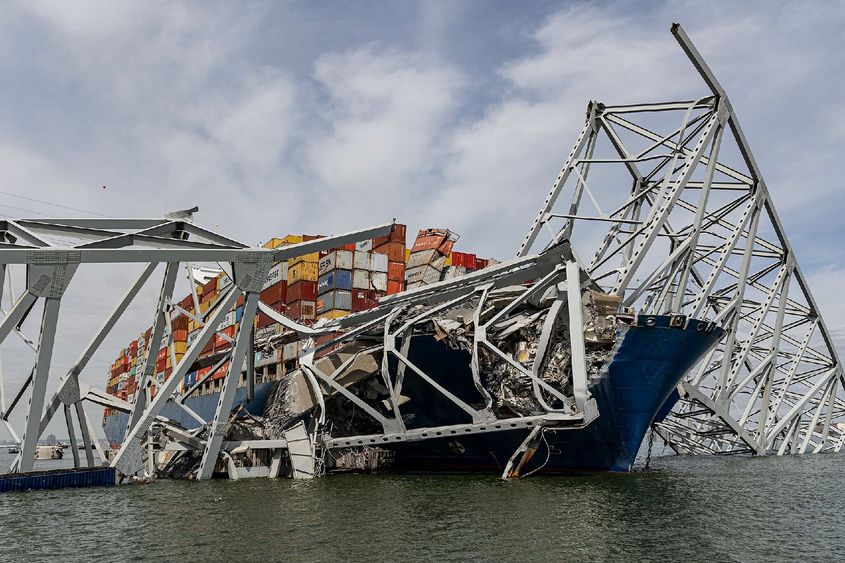
The collapse of Baltimore's Francis Scott Key Bridge disrupted supply chains.
MIDDLETOWN, Pa. — In late March, the cargo ship Dali crashed into Baltimore’s Francis Scott Key Bridge. The bridge, which carried Interstate 695, collapsed, killing six workers.
The collapse also blocked the Port of Baltimore, disrupting cargo ship operations. The port — a major hub for importing vehicles, such as BMW, and for exporting domestic vehicles, such as GM and Ford — reopened in June, after months of shipments being diverted and delayed.
Penn State News sat down with Tony N.K. Lynch, assistant professor of supply chain management in Penn State Harrisburg’s School of Business Administration, to discuss the incident and how it impacted supply chain infrastructure and resilience.
Q: How did the bridge collapse impact supply chain?
Lynch: The bridge collapse gets to the importance of ports and the global supply chain. Ports are our facing infrastructure that interacts with the global supply chain. When that incident occurred, it threw our supply chain, particularly on the East Coast, out of whack.
In my research I focus on issues in supply chain risk as well as transportation policy related to supply chains at the local, national and global levels. Baltimore is a significant port for a number of items. It’s the number one auto port on this coast. It’s also one of the deeper ports on this coast. That’s part of the issue regarding our ports’ infrastructure; not all of them are at the depth that can handle the larger ships. Baltimore is one of the ports that can handle the larger Panamax container ships. When that incident occurred, it meant that the port, of course, would have to close.
Losing the bridge meant that we lose an artery — I-695 — that can lead to significant congestion otherwise, and having to figure out where container ships that would ordinarily come into Port of Baltimore, where they could berth, creates other problems. So, then we are having issues of congestion all the way along the East Coast corridor.
Not to mention so many people were out of work: 15,000 employees work directly in the port, all the other folks that are affected. It has a tremendous ripple effect.
Q: How was the impact handled over the past few months?
Lynch: There was significant coordination — sharing information and resources — between and among the various government entities at the federal and state and local levels. For example, the Army Corps of Engineers focused on removing the debris to reopen the port. State officials worked to recover the missing workers who were working on the bridge on the night of the disaster. Baltimore City officials retained legal counsel to determine who was at fault. The FBI also launched an investigation to determine if there was any criminal activity leading to the crash.
In a way, these efforts were aimed at regaining confidence in our supply chains. There were then and still are now significant deficiencies in our supply chains, primarily the result of under-investment in our ports, such as the minimal automation of our ports compared to other developed nations, and in our road and bridge infrastructure. The Infrastructure Investment Act, which earmarked funds to improve infrastructure across the country and was signed into law in 2021, was a huge help. However, road congestion persists and increases delivery times as well as transportation and logistics costs.
Q: The port has now reopened. Will supply chain continue to be impacted, and how?
Lynch: Yes, supply chains are still affected despite the reopening of the port.
Bear in mind that the bridge is still out and won’t be replaced for some time. That missing link in the port’s logistics operations creates considerable congestion. This quote from Mary Kane, president of Maryland’s Chamber of Commerce, drives home the point: “The port is back. Yes, absolutely. The bridge is not.”
The reopening builds confidence. It is a signal that the government — all those persons involved, including U.S. Transportation Secretary Buttigieg, Maryland Governor Wes Moore and Baltimore Mayor Brandon Scott — are all working to “fix” the problem. But that is merely the tip of the iceberg, so to speak. There are still two big issues. First, here is the issue of traffic congestion created because of the missing bridge. That’s not going away anytime soon. Although the port has resumed operations, the missing Key Bridge creates problems throughout supply chains. It lengthens delivery times. One of the performance measures used is on-time deliveries. It’s going to take longer to move goods because of port congestion — redirected container ships from the Port of Baltimore will have to berth at other East Coast ports, which may not be able to handle the types of cargo normally shipped through the Baltimore port. There is also road congestion: I-695 was a major artery for commuter traffic as well as logistics traffic. While there isn’t data currently available, it follows that a disruption — the loss of the Key Bridge — will have spillover effects.
Second, there’s the issue of the new bridge construction. Even with the opened port, when construction starts, one wonders whether congestion in the channel to the port will hamper port operations.
Our supply chains are functioning, but at a reduced rate given the existing complexities of the missing bridge and traffic congestion.
Q: What does this event say about the importance of supply chain infrastructure? What did we learn?
Lynch: The Dali crashing into and collapsing the Key Bridge exposed the fragility of our supply chains. One incident can severely disrupt operations at several nodes across supply chains. It also highlighted the issue of the resiliency of our supply chains. How quickly can our supply chains respond to and recover from disruptions or disasters? Can we redirect traffic in and out of that port to go to another port and make it easier? Because of the limited or lack of investment in our ports’ infrastructure, many ports are not equipped to berth some of the larger container ships. So, the closure of the Port of Baltimore may force ships with goods destined for the Northeast region to dock at ports further down the east coast, thereby increasing transportation and logistics costs, and ultimately costs for consumers.
The lesson policymakers and decision makers should take away from this incident is contingency planning. The ability to respond to and recover from a significant disruptive event requires advance planning.
Q: What did your students learn from this event?
Lynch: I had visited the Port of Philadelphia with a group of students the week before the Key Bridge collapsed in Baltimore. When it happened, I didn’t have to spur conversation in class, they naturally just started discussing it. When we went to the Philadelphia port, they got to see and examine port operations, so they had a sense of the importance of that port as well as other ports. It led to natural discussion and conversation. That’s knowledge and information you really can’t buy. We were fortunate three container ships had come in and they got to see various terminal operations.
Then the incident occurred and ... it just highlighted the nature of understanding the importance of ports in our global supply chains. Students expressed similar concerns to those expressed by policymakers and practitioners addressing the disaster. The main question was, “What happens next?”